

So in the case, NEMA 17 step angle is 1.8 deg. Steps Per Revolution for a particular stepper motor is calculated using the step angle of that stepper motor. Normally center tap wires left disconnected. Black, Yellow, Green wires are part of first winding where Black is center tap, and Yellow and Green are coil end while Red, White, and Blue is part of a second winding, in which White is center tap and Red and Blue are coil end wires. These wire are connected in two split windings. Wiring diagram for NEMA17 is given below.Īs you can see that this motor has a Unipolar six-wire arrangement.
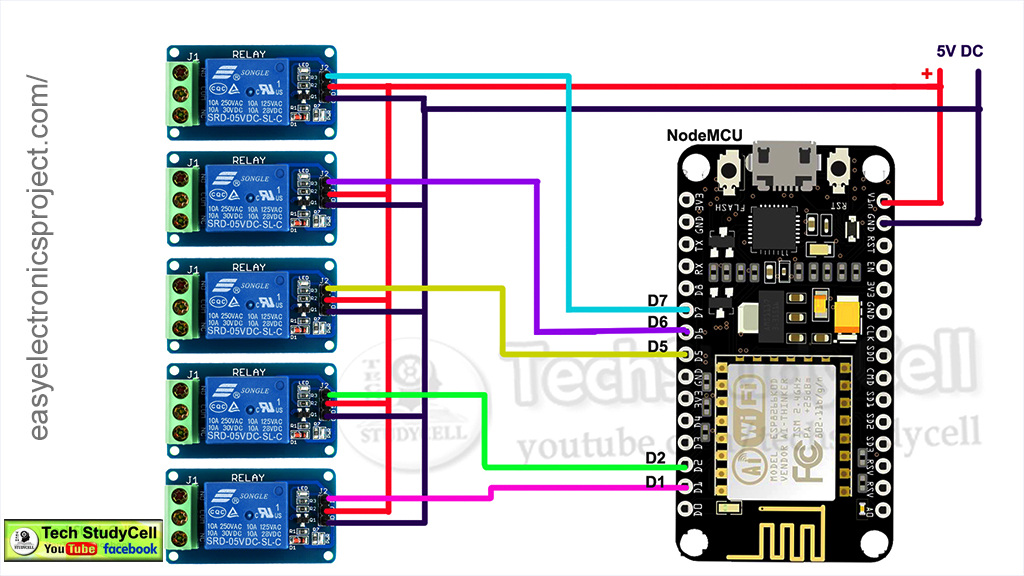
means it covers 1.8 degrees in every step. Stepper motors do not rotate they step, and NEMA17 motor has a step angle of 1.8 deg. It can be operated at a lower voltage, but torque will drop. This motor has six lead wires, and the rated voltage is 12 volt.
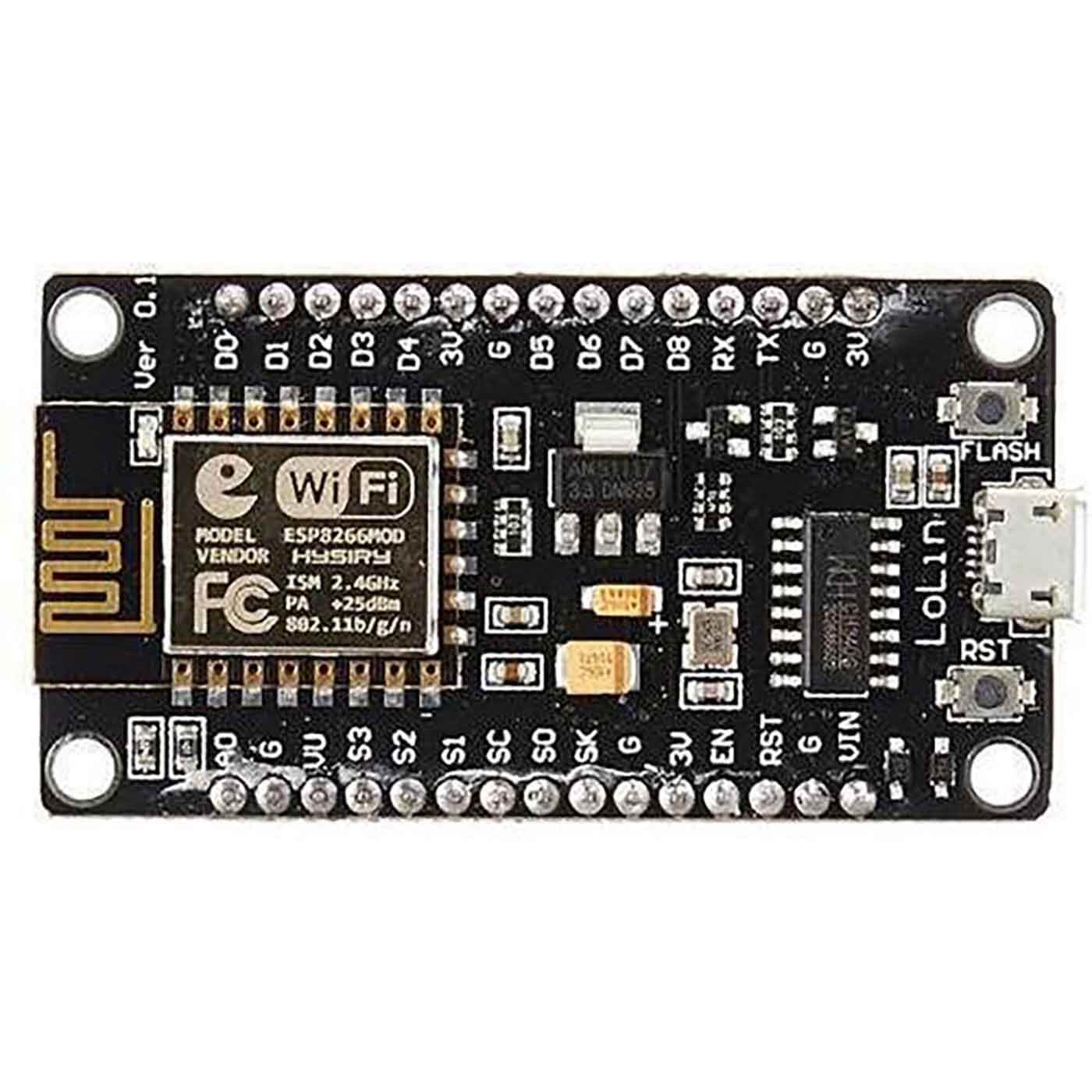
NEMA 17 stepper motor has a 1.7 x 1.7-inch faceplate, and it usually has more torque than the smaller variants, such as NEMA 14. Operation of Nema17 is similar to normal Stepper Motors. Here a potentiometer will also be attached to control the direction of stepper motor. Nema17 stepper motor has higher torque and higher operating voltage than 28-BYJ48. In this tutorial, we are going to control NEMA17 stepper motor using Arduino Uno and A4988 stepper driver module. 28-BYJ48 has relatively lower torque than the other stepper motors like NEMA 14, NEMA17. In our previous project, we controlled 28-BYJ48 stepper motor using Arduino. Stepper motors provide accurate controlling, and can be differentiated on the basis of torque, steps per revolution, and input voltage. A stepper motor is a type of DC motor that works in discrete steps and used everywhere from a surveillance camera to sophisticated robots and machines.
